Our Results
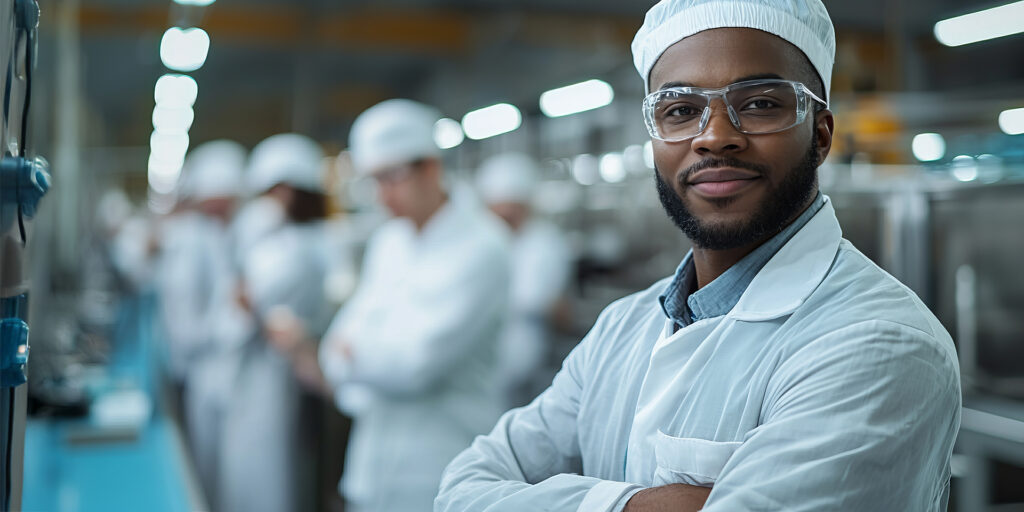
Programs and resources at Food Processing Skills Canada such as FoodAbility, the Student Work Placement Program, and Skills Training Across Canada are available to all Canadian food and beverage businesses and the benefits are impressive. Together with industry partners and program participants we have assessed that skills training and workforce development programs deliver measurable outcomes including improved productivity among individual employees and teams, and improved workplace communication and culture.
Our research has indicated that anticipated outcomes from the Skills Training Across Canada program occur on three levels.
Individual Impact
Skills Training Across Canada (STAC) has significantly enhanced individual participants’ technical skills, social-emotional learning, and leadership capabilities. Graduates reported improved job satisfaction and a continuous learning mindset, with 82% expressing increased job satisfaction and 86% enjoying supervisory-related aspects of their roles more. Key statistics include:
- 42% of graduates use STAC-learned skills daily.
- 96% use these skills at least monthly.
- 98% reported learning things that make them better supervisors.
- 97% gained new knowledge about food safety.
One participant noted, “One of the key takeaways has been the impact of cultivating a positive mindset on both personal well-being and team dynamics. Learning an approach to foster positivity.” These improvements contribute to personal growth and professional effectiveness, fostering a more resilient and adaptable workforce.
Team Impact
At the team level, STAC has led to noticeable improvements in performance, communication, and adaptability. Employers observed enhanced relationships among team members and better feedback mechanisms. Key statistics include:
- 95% of employers noted improvements in providing positive and corrective feedback.
- 84% of graduates observed improved supervisory skills.
- 97% reported better understanding of how to support team training and development.
A participant shared, “Having a positive attitude at work has an immediate effect. Emotional intelligence is amazing.” These changes have created a more supportive and cohesive workplace environment, enhancing overall team dynamics and productivity.
Organizational Impact
The organizational benefits of STAC are evident in increased productivity, improved workplace culture, and higher retention rates. Employers reported significant impacts on employees’ interest in company performance and training opportunities. Key statistics include:
- More than two-thirds of companies noticed improvements in retention and absenteeism.
- 95% of employers observed improvements in workplace communication and culture.
- 98% of graduates would recommend the leadership courses to other supervisors.
One employer stated, “The comprehensive curriculum, including topics like Food Safety, Emotional Intelligence, Social Emotional Learning, and Leadership for Supervisors, provided valuable skills and knowledge to enhance our employees’ abilities and contribute to our overall success.” These outcomes underscore the program’s value in driving long-term organizational success and fostering a culture of continuous improvement and engagement.
Return On Investment
In an effort to directly quantify program benefits for companies, Food Processing Skills Canada initiated a return on investment analysis for participating businesses in the Skills Training Across Canada program and the returns proved to be significant. Preliminary estimates show that every $1 invested in training by employers produces a return of $20 or more in beneficial outcomes for the company.
The initial mini cost-benefit analysis for calculating the ROI for STAC utilizes data from evaluations, literature, and Stats Can, with each variable in the equation adaptable to different contexts or situations. This process is ongoing as more data is collected.
Scenario 1: Maximizing ROI through Training in Small Food Processing Operations
For small food processors with a staff of 15, including 2 supervisors and 10 frontline workers, investing in training programs like STAC can yield significant returns. With annual sales of over $2 million, and over $200,000 invested in food safety, GMPs, and QA/QC processes, the potential benefits far outweigh the costs.
Key Highlights:
- Actual Costs: $4,500 (including training coordination and participant time).
- Potential Benefits: $94,073, including:
- Cost avoidance from reduced supervisor turnover: $26,325.
- Cost avoidance from reduced frontline worker turnover: $17,748.
- Increased productivity leading to a 2% boost in sales: $40,000.
- Enhanced effectiveness in food safety and related areas: $10,000.
Scenario 2: Maximizing ROI for Medium-Sized Food Processing Operations
For medium-sized food processors with 75 employees, including 5 supervisors and 60 frontline workers, investing in training programs like STAC can achieve transformative results through training. With annual sales of over $10 million, and over $600,000 invested in food safety, GMPs, and QA/QC processes, the ROI is compelling.
Key Highlights:
- Actual Costs: $11,000 (including training coordination and participant time).
- Potential Benefits: $259,390, including:
- Cost avoidance from reduced supervisor turnover: $52,650.
- Cost avoidance from reduced frontline worker turnover: $88,740.
- Increased productivity leading to a 1% boost in sales: $100,000.
- Enhanced effectiveness in food safety and related areas: $18,000.
We are still in the early phase of analysis, but the results are as expected. When a business invests in its people the benefits are felt broadly and deeply.