A Maintenance Manager plans, organizes, directs, controls and evaluates the maintenance department within food and beverage manufacturing facilities. This position commonly reports to the Plant Manager, Plant Management Team or possibly Engineering Managers.
The overall goal is to ensure the equipment, machinery and facilities are not only working and regularly maintained, but also are safe for the team working in them and ensure the safety of the final food products. The Maintenance Manager leads a team of technicians and supervisors who perform checks, documentation, report concerns and help keep the daily operations of the facility on track.
As a Maintenance Manager you will design and implement a robust maintenance program that increases the overall reliability and productivity of the plant while meeting all health and safety compliance requirements.
Although it may not seem like it, the maintenance team plays a key role in helping the plant achieve and maintain food safety certifications!
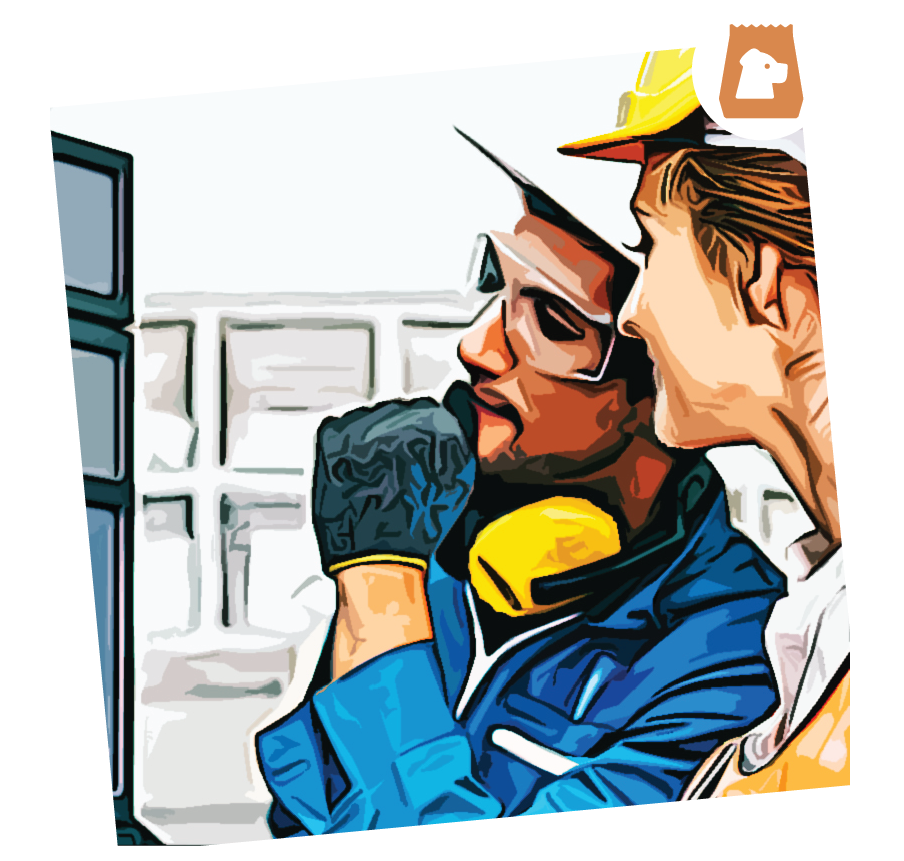
THE WORK ENVIRONMENT
FACT: A career as a Maintenance Manager is highly transferable, as all facilities in and out of the food manufacturing industry require Maintenance Managers to keep their facilities in compliance with regulations and safe for all individuals using the facilities.
MAINTENANCE MANAGER SALARY
Low Range
$22 per hour
Average
$36 per hour
High Range
$58 per hour
Typically a Maintenance Manager is a full-time permanent salaried position. Starting pay for this occupation is highly dependent on the amount of education and experience you bring to the table, as well as the scope of the processing operations that you’ll be responsible for. Salaries for this position can exceed $120k based on experience level.
Employers are competing to bring you on board, and encourage interest in their companies by touting organizational missions, visions and philosophies. Many employers offer competitive benefit and compensation packages including health and wellness benefits, dental, vision care, RRSP contributions, and paid vacation.
Some cool perks seen for this role include annual bonuses, an allowance for cars or cell phones, and learning opportunities. Education reimbursement and access to in-house university tools with ongoing learning are also popular incentives.
MAINTENANCE MANAGER JOB DUTIES
Some of the responsibilities of the Maintenance Manager include:
- Develop and implement a robust preventive maintenance program for the facility. Using your technical expertise, take into consideration various nuances of the plant and historical operations and failures.
- Demonstrate an ongoing commitment to the improvement of plant operations, product quality and food safety.
- Build strong working relationships with all departments to better understand the daily maintenance support needs.
- Plan, organize, direct, control and evaluate all maintenance and repair of the establishment’s machinery, equipment and electrical and mechanical systems. Also known as preventative maintenance.
- Work with the team to increase the overall efficiency of the plant reducing downtime, helping to meet production targets, increasing productivity, achieving environmental and company goals.
- Plan and manage the facility’s operations budget and schedules to ensure the smooth running of ongoing projects.
- Develop and maintain excellent relationships with manufacturers, suppliers and contractors for equipment quotes, maintenance, warranty modifications and improvements.
- Administer contracts for facility-related projects, supplies and services. As well as facilitating any larger construction projects to modify the facility.
- Create schedules and procedures for safety inspections.
- Providing leadership, direction and coaching to all employees within the department.
- Hire and oversee training and supervision of maintenance staff and technicians.
- Ensure that the plant is in compliance with all laws and regulations pertaining to its operations.
- Work with the team to meet all relevant food safety standards, good manufacturing practices, and quality assurance requirements – helping to achieve third-party certifications.
BECOMING A MAINTENANCE MANAGER
Every plant needs to have a Maintenance Manager, so you’ll find employment opportunities in all areas of the food and beverage manufacturing industry. This career is also transferrable to a number of different industries outside of food manufacturing, with the right qualifications finding a career opportunity should be relatively easy – it’ll just be a matter of picking which benefits you like most!
Compliance with food safety regulations as well as health and safety regulations are ongoing requirements for food manufacturing facilities, as such there’s always a high demand for someone who has the skills to do the job.
This is a technical role requiring a large capacity to manage, plan resources and lead teams. Organizations will accept a variety of qualifications for the role including those with an engineering background, industrial electricians, and millwright mechanics, therefore higher education and qualifications will provide you with more opportunities for advancement. Employers sometimes have difficulties finding individuals with the right qualifications for the role and thus are willing to promote from within for those who show a keep interest in learning and promote a positive team environment, putting safety as a top priority.
You’ll be working with many different team members including senior management, the maintenance team, auditors, third party consultants, various vendors, as well as training team members in the plant – possessing leadership qualities can’t be underestimated when it comes to success and advancement.
Many employers are seeking individuals who have a bachelor’s degree in engineering, mechanics, electricity, automation, science, or in a related field. They will also accept diplomas in these areas or a combination of technical skilled trade qualifications, technical certificates, etc. Experience is also highly valuable in this role and employers will also accept a combination of education and experience, most are seeking a minimum of 3 to 5 years of experience, with larger opportunities seeking a minimum of 8 to 10 years of experience.
Strong verbal and oral communication skills are required to lead, manage and coach a team of people. Progressive leadership and management experience are very important and highly attractive qualifications for employers. If you’re lacking experience in this area, there are many short programs available throughout Canada to help you brush up on your leadership skills.
Knowledge of food manufacturing regulations is highly important and attractive but not necessary to be hired for the position, although they will be a mandatory requirement of the job. You may want to consider some short courses in food industry such as:
- Good Manufacturing Practices (GMPs)
- Introduction to Internal Audits in Food Manufacturing
- Introduction to Preventive Control Plans
- Traceability and Recall in the food manufacturing industry
- Hazard Analysis Critical Control Points (HACCP)
- Food Safety and Food Spoilage
- Continuous improvement and Lean Manufacturing